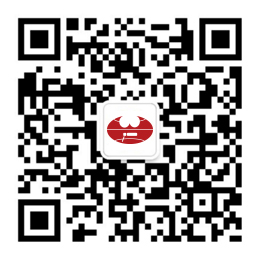
- 021-66798861-0
Editor's note
At the beginning of 2020, due to the impact of the new crown pneumonia epidemic, my country's chemical equipment industry has been greatly impacted. However, industry companies are united and have devoted themselves to the flood of support for the fight against the epidemic with unparalleled courage. While doing a good job in epidemic prevention and control, we are also actively planning to promote the resumption of work and production, so that industries that have experienced frost and snow in the epidemic can breathe and recover. Throughout the year, the chemical equipment industry has been striving to move forward under the background of epidemic prevention and control, and has maintained a steady and progressive development trend, especially in the fields of high-end equipment manufacturing and other fields. Smart Manufacturing Weekly has maintained a consistent focus on this and conducted a comprehensive report. The editorial department has specially sorted out the top ten news of the chemical equipment industry in 2020 for readers.
1. The ultra-large volume LNG storage tank technology passed the identification
On February 10, 2020, the design and construction technology of super-large liquefied natural gas (LNG) storage tanks (200,000 to 270,000 cubic meters of volume) of China National Offshore Oil Corporation achieved smooth results Through expert appraisal, it marks that CNOOC's core technology system of CGTank storage tank has fully realized the independent creation and development, which fills the gap of domestic super-large-volume LNG storage tank design and construction technology, and provides a basis for promoting the large-scale construction of LNG super-large-volume storage tank. Reliable technical support.
The self-innovated super-volume LNG storage tank can greatly reduce the construction cost of LNG storage tank, which is about 15%~20% lower than the previously introduced foreign technology. LNG super-capacity storage tanks can greatly improve the storage turnover capacity of the receiving terminal, which is of great significance for realizing the intensive construction of natural gas storage facilities, enhancing the peak-shaving capacity of natural gas storage and promoting the coordinated development of the upstream and downstream of the LNG industry chain. Taking the storage tank of 270,000 cubic meters as an example, the gas storage capacity of a single tank can supply more than 22 million people in Beijing for more than two months.
2. Chemical equipment companies plan to resume work
At the beginning of 2020, the new crown pneumonia epidemic swept the world, and my country's chemical equipment manufacturing enterprises suffered a lot. In the process of comprehensively combating the epidemic, chemical equipment enterprises have gradually resumed work and production.
February 10 is the first day of resumption of work after the Jiangsu Provincial People's Government extended the Spring Festival holiday. On the premise of properly taking protective measures, Jiangsu valve enterprises try to reduce the negative impact of epidemic prevention and control on industry production as much as possible. In good health; on the other hand, timely coordinate and solve difficulties and problems in the resumption of work and production, and fully restore normal production. On the first day of resumption of work in the province, CNNC Suvalve Technology Industrial Co., Ltd., Suzhou Neway Valve Co., Ltd., Jiangsu Suyan Valve Machinery Co., Ltd., Yangzhou Power Equipment Repair Factory Co., Ltd., Jiangsu Shengtai Valve Co., Ltd., Jiangsu Yivalve 15 major key enterprises including Co., Ltd. have resumed production one after another. On February 11, Jiangsu Shentong Valve Co., Ltd., Suzhou Douson Valve Co., Ltd., Jiangsu Rongyuan Casting Industry Co., Ltd., Xipai Group Co., Ltd. and other companies also opened their doors one after another.
On March 9, the resumption rate of industrial enterprises above designated size in Shenyang reached 98.6%. Among them, the resumption rate of equipment manufacturing enterprises represented by Shengu Group reached 99.3%, and the resumption rate of petrochemical enterprises represented by Shenyang Chemical reached 98.9%. Shenyang Municipal Bureau of Industry and Information Technology also formulated and issued the "Implementation Plan for the Resumption of Work and Production of Industrial Enterprises Above Designated Size in Shenyang", built a "Shenyang Industrial Enterprise Resumption of Work and Production Platform", and more than 140 "corporate stewards" stationed in 330 key industries Enterprises, implement online and offline precise assistance, and scientifically guide enterprises to resume work.
On April 2, Sinopec Petroleum Machinery Co., Ltd. successfully resumed work and production, and also drove more than 50 affiliated enterprises in Hubei Province to form a "point-like resumption of work" to "full chain" "Resumption of work" situation, to speed up the resumption of production and production of the province's oil and gas equipment industry chain.
3. Automatic welding technology for fillet welds in in-service pipelines is applied
On June 15th, the automatic fillet welding technology of in-service pipelines realized industrial application for the first time in the China-Myanmar pipeline (Guizhou section), marking that this technical difficulty has been successfully overcome. , and achieved zero breakthrough in this field in China. This on-site application is a strong alliance between China Petroleum Pipeline Bureau Engineering Co., Ltd. and Southwest Pipeline Company in the field of scientific research and development. Technical Support.
This technology is the "stuck neck" link in the automatic welding technology of oil and gas pipelines in service. In the construction of automatic welding of pipelines in service, there is usually an uneven gap of 1 mm to 5 mm at the connection between the maintenance and repair pipe fittings and the pipeline in service. Using the traditional manual arc welding welding process, the quality and safety risks are high, while the use of automatic welding The key technology is still at the bottleneck. In order to achieve a breakthrough, the research team tested more than 60 test pieces after 6 months of metallographic experiments on fillet welds, and worked out a set of welding process parameters suitable for different welding positions and different pairs of gaps, and successfully solved the problem. While ensuring quality and safety, efficiency is greatly improved, and personnel costs are also greatly reduced.
This on-site application selects pipelines in mountainous areas of Guizhou Province with complex climatic environment, geological conditions and difficult operation. The results are highly pertinent and directional. , which fully confirms that the technology has achieved full compatibility in construction conditions, pipeline materials, construction techniques and media properties.
4. The first aromatic type moving bed aromatization unit was put into operation
On July 8, the Petrochemical Research Institute and Guangzhou (Luoyang) Engineering Co., Ltd. jointly developed a 500,000-ton CNOOC Ningbo Daxie Petrochemical Co., Ltd. /year The reaction unit of the moving bed light naphtha aromatization unit began to feed, and qualified products were produced on July 10. On July 12, the catalyst continuous regeneration system was successfully put into use, marking the world's first company with completely independent intellectual property rights in my country. A set of aromatic hydrocarbon type moving bed light naphtha aromatization unit was successfully started.
This technology mainly uses C₃~C₇ mixed light hydrocarbons as raw materials to produce benzene, toluene and mixed xylene, and by-product hydrogen, which aims to open up a new way for the efficient utilization of light hydrocarbons technical approach. Back in April 2016, the project entered the research phase. In November of that year, after the project was approved, the two sides cooperated closely and started the research and development of the first set of industrial equipment. In order to overcome the shortcomings of fixed-bed light hydrocarbon aromatization, such as low aromatic hydrocarbon yield, high carbon deposition, and short operation period, and at the same time meet the requirements of moving bed process cycle and promotion. On the basis of summarizing the experience of the previous generation of light hydrocarbon aromatization process technology, the Research Institute of Petrochemical Science has creatively developed a new generation of non-precious metal, polymer sieve content small spherical catalysts with high reactivity, high aromatics selectivity and crushing strength. It has the characteristics of high circulation fluidity, excellent hydrothermal stability, anti-carbon deposition performance and good regeneration performance.
5. Commissioning of the largest domestic ethylene cracking gas compressor
On July 9th, the largest domestic 1.3 million tons/year ethylene cracking unit was built and developed by Shenyang Blower Group Co., Ltd. for Zhongsha (Tianjin) Petrochemical Co., Ltd. The nitrogen test run of the air compressor unit was successful once. The amplitude of the unit is far better than the international standard of 25.4μm, less than 1/4 of the diameter of the hair, and other performance parameters have reached the high-quality level.
Zhongsha (Tianjin) Petrochemical's 1.3 million tons/year ethylene plant cracking gas compressor unit is one of the "Big Macs" among all the products developed by Shengu. The maximum impeller diameter of the compressor unit is 1.4 meters, the total height of the unit is 5.7 meters, the total length of the unit is 25 meters, and the weight of the whole unit is close to 500 tons. The successful commissioning of this project indicates that Chinese enterprises have fully possessed the ability to "run side by side" with international first-class enterprises in terms of the core key equipment of ethylene plants of 1 million tons and above, and are moving towards "leading"; While solving the problem of "stuck neck" in the development of my country's petrochemical industry, reducing the difficulty of customer procurement and saving procurement costs, it also provides a guarantee for the stable, safe and long-term high-quality operation of ethylene plants.
6. The first domestic BOG helium extraction device passed the identification
On October 17, the BOG (flash gas) helium extraction device demonstration project jointly developed by Beijing Zhongke Fuhai Cryogenic Technology Co., Ltd. and Ningxia Shenran Zhongyuan Natural Gas Co., Ltd. Ningxia Yanchi site passed the technical achievement appraisal. The expert group agreed that the project, relying on the technology of the Institute of Physics and Chemistry of the Chinese Academy of Sciences, realized the first demonstration operation of BOG production of liquid helium products in China, filling the domestic gap. The project has explored a helium extraction road suitable for my country's national conditions, which is conducive to solving the "stuck neck" problem of my country's strategic helium resource shortage. It is recommended that the technological achievements be industrialized and promoted as soon as possible.
According to the on-site test results, the helium purification and liquefaction unit of BOG helium extraction device has reached a helium liquefaction rate of 42.9 liters/hour, and the performance index has reached or exceeded the requirements specified in the process design. Requirements; the device has strong adaptability to changing working conditions, and can cope with the fluctuation of BOG feed gas composition, especially the unfavorable conditions that the composition of hydrogen and helium seriously deviates from the design working conditions; the self-developed turboexpander based on high-speed helium gas bearing and internal purification The key technology of the helium liquefier has high reliability. The BOG helium extraction device has an advanced process route, a high degree of automation, and reliable and stable operation.
The expert group stated that the successful commercial demonstration operation of LNG-BOG cryogenic helium extraction equipment in Ningxia Yanchi not only realized the national production of large cryogenic equipment, but also broke foreign technical barriers; On the basis of ensuring the safe and stable production of existing LNG plants, reducing operating costs and achieving economic breakthroughs are well recognized by the owners of LNG plants and provide an important reference for other LNG plants in the Greater Ordos area to replicate the BOG helium extraction project.
7. The semi-rich amine liquid pump is made in China
On November 28, the domestically produced semi-rich amine liquid pump developed by Sinopec Puguang Gas Field Branch was successfully installed in the third combined unit of the natural gas purification plant, and the conditions for operation were met. The equipment's process parameters, sealing performance and other indicators have reached the industry-leading level, which can perfectly replace the original imported equipment.
The semi-rich amine liquid pump is the key device of the purification process. It mainly transports the semi-rich amine liquid from the exhaust gas absorption tower to the primary main absorption tower for regeneration. It restores the "detoxification" function again. There are thousands of internal parts of semi-rich amine liquid pump, and the types involved are more and more complicated, and it is extremely difficult to tackle key problems.
When Puguang Gas Field Branch started production in 2009, it purchased 24 semi-rich amine pumps with high safety factor from foreign companies at high prices. However, with the continuous high-load production of gas fields, these "delicate bodies" have been "injured" one after another, and various failures have gradually appeared since 2012. At the end of 2017, Sinopec Group Corporation officially designated the project of "localized development of high-pressure multi-stage centrifugal pumps for natural gas purification devices" as a major project in the "13th Five-Year Plan", and handed over to Puguang Gas Field to tackle key problems.
Puguang Branch has strengthened fine management and carried out localization research simultaneously to completely solve the "root cause" that has restricted the gas field for 8 years. In the process of implementing localized research, each operation problem was solved one by one, especially in the problem of frequent failure of mechanical seals. After hundreds of experiments, the research team finally developed a localized double-end machine with excellent anti-vibration performance. seal. The axial size of the matching ring in the domestically produced semi-rich amine liquid pump is only 2.7 mm, and the size of the same type of product from an advanced foreign company is 3.5 mm, which makes the axial size of the matching ring of the key device of the equipment 1.2 mm smaller than that of the imported equipment. It ensures the smooth operation of the equipment and improves the service life. This also marks that the industry problem of "better compensation for rotor assembly runout and verticality error" has been completely overcome.
8. Chajiawan Village commemorates the 50th anniversary of the drying industry
On November 11th, Chajiawan Village, Zhenglu Town, Tianning District, Changzhou City, Jiangsu Province held a grand ceremony to commemorate the 50th anniversary of the drying industry.
In the past 50 years, the industrial development of Chajiawan has grown from nothing, from small to large, from simple to refined, all the way through trials and hardships, until the industrial drying equipment at home and abroad The products and equipment of Chajiawan Village can be seen in the market and application fields, and they have a certain market brand and status. The industrial industry of Chajia Village started from a pair of scissors, two hammers, and three broken houses in the early 1970s. From a humble project information breakthrough, today it has developed into 681 factories, more than 13,000 employees, 30 It is one of the four pillar industries of Zhenglu Town with an industrial output value of more than 100 million yuan.
In terms of the current domestic and foreign drying equipment industry market conditions, the competition pattern of several large-scale domestic drying equipment industries has been broken, and the number of manufacturers has grown from several to hundreds. , The development speed is very fast, the product technology level is rapidly improved, and the gap with foreign products is narrowed. The development process of my country's new drying equipment industry has received much attention from international counterparts. 50 years ago, the first drying plant in China started from Chajiawan and developed into a drying town with hundreds of drying enterprises in just a few decades. In order to promote the development of the local industrial economy and China's drying industry, it has made a contribute.
At present, the drying equipment manufacturing industry at home and abroad is changing. The main domestic production enterprises are highly concentrated, and the gap between the technical level, craftsmanship and appearance of the products is gradually narrowing, and the personalized needs of users are becoming more and more It has become more and more prominent, and the market demand has developed from the demand of quantity to the demand of quality, and the requirements for complete sets, continuous production and automation of large-scale drying equipment are higher. Fan Binghong, vice president of the Drying Equipment Industry Branch of China General Machinery Association and chairman of Changzhou Fanqun Drying Equipment Co., Ltd., said that the drying equipment industry is now entering a new stage of development, breaking through its own limits and keeping up with the development of the industry, which will drive drying equipment. and industrial upgrading of applications. Accelerating technological iteration and accelerating industry cross-border integration are the keys to achieving the sustainable development of the drying industry, and high efficiency, greenness and sustainability have become the core behind this development trend.
9. The world's first multi-nozzle semi-waste boiler gasifier test run
On December 10th, Shandong Energy Group Yanzhou Coal Industry Yulin Energy Chemical Co., Ltd., which was EPC general contracted by China Tianchen Engineering Co., Ltd., a subsidiary of China Chemical Co., Ltd. The F# gasifier with a daily processing capacity of 2,000 tons of coal in the project (DMMn) was successfully put into operation at one time. This means that the world's first multi-nozzle opposed semi-waste boiler (waste boiler - chilling) gasifier has officially entered the stage of trial operation with load.
This project is currently the largest polymethoxy dimethyl ether project in China, with an annual output of 500,000 tons of polymethoxy dimethyl ether and an annual output of 900,000 tons of supporting materials. Coal to methanol project. As of December 10, all methanol projects have been completed and put into use. During the "13th Five-Year Plan" period, the energy group's coal gasification field led the industry development with technological innovation. The multi-nozzle opposed semi-waste boiler gasifier was jointly developed by the former Yankuang Group and East China University of Science and Technology. The inner diameter is 4.2 meters, the weight is 737 tons, and the daily coal processing capacity is 2,000 tons. It has the advantages of high carbon conversion rate and low raw material consumption. Compared with the traditional chilled gasifier, the energy utilization efficiency is greatly improved. The high-temperature syngas recovers most of the sensible heat through the waste boiler in the gasifier, and produces about 100 tons of 9.8 MPa high-pressure steam per hour. Energy conservation and emission reduction development policies.
Compared with the traditional chilled gasifier, the semi-waste boiler gasifier is equipped with a radiant waste boiler, which increases the overall thermal efficiency of the device by about 5% and reduces the comprehensive energy consumption by about 10%. It can efficiently utilize the sensible heat carried by the high-temperature synthesis gas produced by the gasification combustion chamber, and the high-pressure saturated steam generated can be used to drive large-scale steam turbines after superheating, and the energy efficiency of the device is increased by about 10%. The effect on the economic benefits of the project is particularly obvious.
10. Breakthrough in slurry bed hydrogenation equipment technology
On June 1st, the world's first 3,000-ton super slurry-bed forging-welding hydrogenation reactor manufactured by China First Heavy Industry Group Dalian Nuclear Power & Petrochemical Co., Ltd. was completed, shipped, and put into operation. sail. The successful manufacture of this equipment has once again set a new record for the manufacture of forge-welded hydrogenation reactors in the world.
The 3,000-ton super slurry-bed forge-welded hydrogenation reactor is currently the largest refining and chemical integration project under construction in the world—Zhejiang Petrochemical 40 million tons/year refining and chemical integration The core equipment of the second phase of the project. The equipment has a single weight of over 3,000 tons, a total length of over 70 meters, an outer diameter of 6.15 meters, and a wall thickness of 0.32 meters. After the project is completed, it will further optimize the layout of my country's petrochemical industry, accelerate the construction of seven world-class petrochemical industry bases in China, and play a positive role in promoting the vigorous development of the "Belt and Road" and "Yangtze River Economic Belt".
On December 31st, Sinopec Maoming Petrochemical 2.6 million tons/year slurry bed residue hydrogenation unit was successfully put into operation, marking the world's advanced slurry bed residue hydrogenation The technology realizes industrial application in my country. The unit is the world's largest and the first domestic slurry bed residue hydrogenation unit. It adopts Italian ENI-EST process technology, which can efficiently convert heavy and inferior crude oil into clean oil products, with strong conversion capacity and high light oil yield. Significant technical advantages, can better adapt to changes in the nature of raw materials, and realize the use of "worst residual oil" to produce "best quality products".
As the core unit of Maoming Petrochemical's product structure optimization project, the 2.6 million tons/year slurry bed residue hydrogenation unit uses inferior vacuum residue and catalytic cracking oil slurry as raw materials , After hydrothermal cracking reaction, liquefied gas, chemical raw materials, heavy naphtha, diesel oil, vacuum wax oil are produced. The designed light oil conversion rate of the device is 94%, which can convert low value-added products such as asphalt and coke into clean oil products with high value-added such as gasoline, coal and diesel. The yield of light oil in the whole plant is greatly improved, and the value of petroleum resources is maximized use.
SMC's product trademarks include: Inconel, Inco-Weld, Monel, Ni-Rod, Incoloy, etc.
Lincoln's product trademarks include: Tech-Rod,Excalibur
Arcos's product trademarks include: Arcosr
VDM's product trademarks include: VDM
Oxford's product trademarks include: Oxford Alloy
AMF's product trademarks include: AMF
Siegmund's product trademarks include: Siegmund
ITW's product trademarks include: Miller
Copyright © 2021 上海韦泰工业器材有限公司 All Rights Reserved 沪ICP备05035196号
517900685@qq.com
18221020274
info@wel-tech.com
021-66798861-0
message